A7 - Dynamic Process Forces (funding period 2)
Improvement of combined cutting and deep drawing processes by means of overlaying dynamic process forces
Project Status: finished
Last Update: 23.01.2017
Members
Sheet-bulk metal forming is a forming process with two and triaxial state of stress and a triaxial dimensional change by using of sheet material. The part itself will be manufactured by deep drawing and the gearing will be produced with bulk forming in a combined process at room temperature. With a new possibility of superimposing oscillations the process forces will be reduced, the part quality will be improved and the process limits are broadened.
The main objective of the second funding phase is the increasing complexity of oscillation-superimposed sheet-bulk metal forming (SBMF) by developing a new multistage forming process. The process consolidates the metal forming techniques from the first funding phase to a process chain. The last operation of the chain is sizing of component. Figure 1 depicts the process chain and the demonstrator.
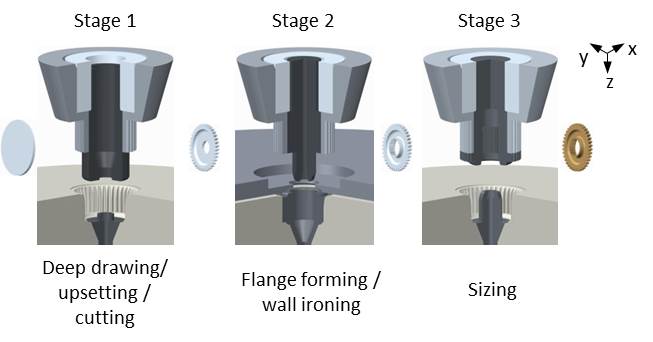
Fig. 1: Process Chain
Furthermore, a numerical model for simulation of oscillation-superimposed SBMF is developed (Figure 2). The numerical model is expected to describe true stress of investigated material depending on frequency, amplitude, temperature, strain and strain rate by means of oscillation-superimposed fundamental experiments (tensile and compression tests).
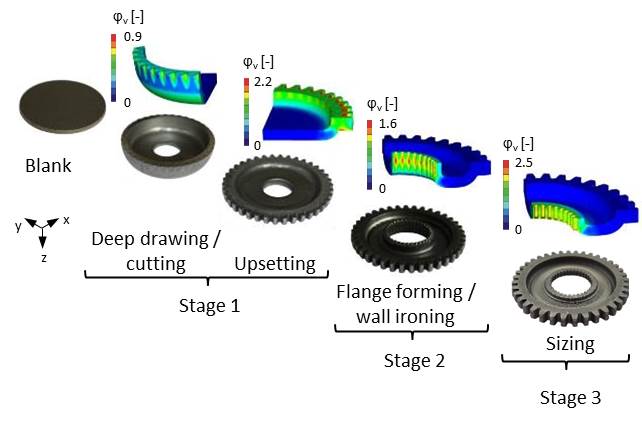
Fig. 2: Process chain
Consequently, the following aims were derived:
- Development of a multistage SBMF process in consideration of preliminary work (shearing) and reworking (sizing)
- Investigation of basic parameters for characterization of oscillation-superimposed SBMF processes.
- Identification of the interactions of frequency on the multistage SBMF processes.
- Process optimization by use of tailored blanks and tailored surfaces.
- Systematic evaluation of the multistage processes by cause-effect-chain.
At the beginning of the project, the material characterization and modeling are in the foreground. Therefore, the hydraulic oscillation system from the first founding phase is integrated in the material characterization process. Using an energy approach, the oscillation-dependent lowering of stress compared to conventional quasi-static and dynamic received characteristics are determined. Furthermore, the temperature effects are considered. In addition, the exciting friction models for numerical simulation of superimposing of oscillation are parameterized by using the results of the oscillation-superimposed flat compression tests (Fig. 3). Moreover, the flat compression test enables the classification of the surface structures and the coating. The developed models are parameterized by use of the energy approach and used for material flow simulation. Thus, the oscillation-superimposed SBMF processes can be estimated realistically.
Based on the SBMF fundamental experiments from the first funding phase, investigations in the second funding phase are evaluated in a process. The assembly of several design elements from second funding phase is realized in the new multistage SBMF process.
In order to use the mathematical-empirical material approach, the constitutive equation and the friction law are parameterized. Furthermore, the produced components are investigated for verification. Additionally, the grain structure and the residual stress of the components, and the material characterization specimen for representation of the oscillation-superimposed effects are investigated.
For material flow and tools optimization surface structure and coating are at first classified by flat compression test. After that, the surface structure and coating are integrated in the new SBMF process to verify their expedience. Based on the investigations from the first funding phase a requirements profile is created. The requirements profile enables the usage of tailored blanks for material flow optimization in a multistage oscillation-superimposed process.
Concluding, the results are depicted in cause-effect-chain.
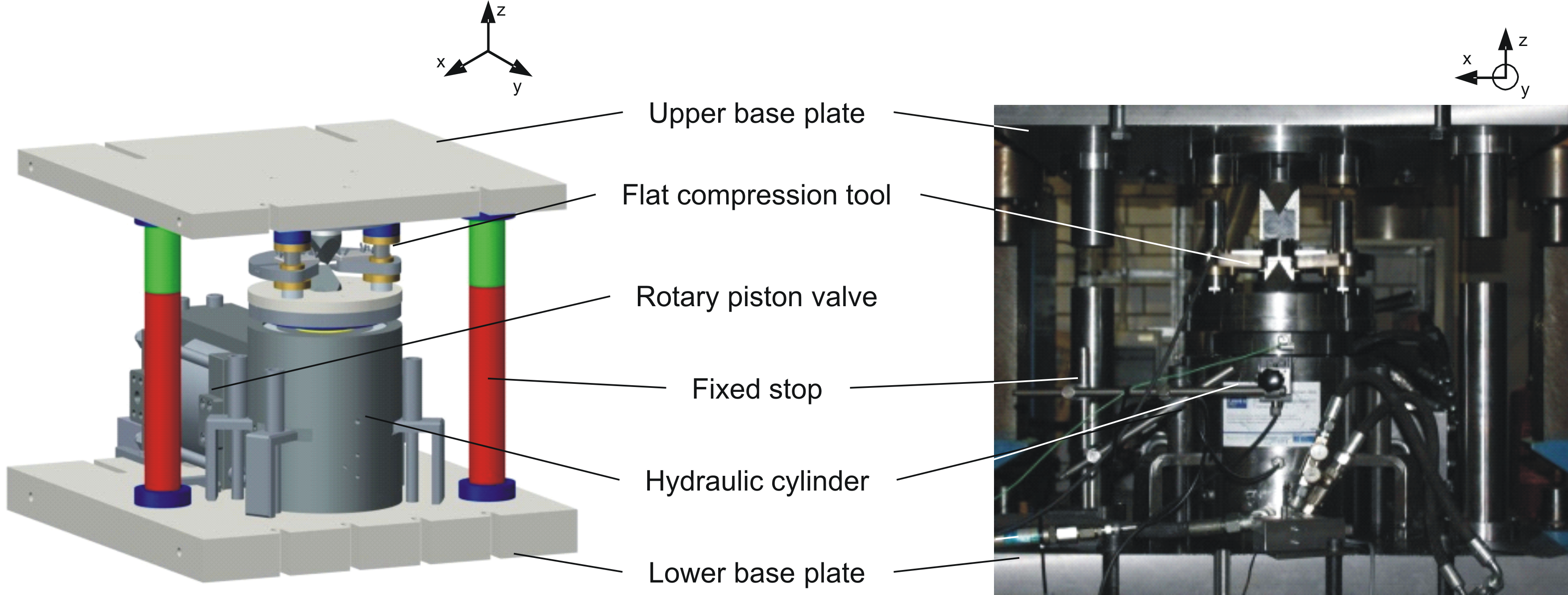
Fig. 3: Flat compression test tool
Working Groups
Publications
2016
- Gröbel, D.; Schulte, R.; Hildenbrand, P.; Lechner, M.; Engel, U.; Sieczkarek, P.; Wernicke, S.; Tekkaya, A.; Behrens, B.; Hübner, S.; Vucetic, M.; Koch, S.; Merklein, M.: Manufacturing of functional elements by sheet-bulk metal forming processes. In: Production Engineering, 10(2016)1, pp. 63-80
- Behrens, B.; Bouguecha, A.; Vucetic, M.; Chugreev, A.; , .: Advanced Finite Element Analysis of Die Wear in Sheet-Bulk Metal Forming Processes. In: ESAFORM (Edt.): (2016), Nante, Frankreich, accepted
- Matthias, S.; Loderer, A.; Koch, S.; Gröne, M.; Kästner, M.; Hübner, S.; Krimm, R.; Reithmeier, E.; Hausotte, T.; Behrens, B.: Metrological solutions for an adapted inspection of parts and tools of a sheet-bulk metal forming process. In: Production Engineering, 10(2016)1, DOI 10.1007/s11740-015-0647-2, pp. 51-61
- Isik, K.; Gerstein, G.; Schneider, T.; Schulte, R.; , .; Clausmeyer, T.; Nürnberger, F.; Vucetic, M.; Koch, S.; Hübner, S.; Behrens, B.; Tekkaya, A.; Merklein, M.: Investigations of ductile damage during the process chains of toothed functional components manufactured by sheet-bulk metal forming. In: Production Engineering, 10(2016)1, pp. 5-15
2015
- Behrens, B.; Hübner, S.; Vucetic, M.; Koch, S.; Denkena, B.; Grove, T.; Lucas, H.; Tillmann, W.; Stangier, D.; Hausotte, T.; Loderer, A.: Prozessauslegung und Untersuchung von geschliffenen und CrAlN / CrAlCN-beschichteten Werkzeugoberflächen mittels schwingungsüberlagertem Flachstauchversuch für die Blechmassivumformung. In: Tekkaya, A. E.; Liewald, M.; Merklein, M.; Behrens, B.-A (Edt.): Tagungsband zum 18. Workshop Simulation in der Umformtechnik & 3. Industriekolloquium Blechmassivumformung 2015 - DFG Transregio 73, (2015), Aachen: Shaker Verlag, pp. 173 - 192
- Behrens, B.; Bouguecha, A.; Vucetic, M.; Hübner, S.; , .; Koch, S.: Numerical and experimental investigations of multistage sheet-bulk metal forming process with compound press tools. In: Key Engineering Materials, 651(2015), Trans Tech Publications, Switzerland, pp. 1153-1158
- Koch, S.; Vucetic, M.; Hübner, S.; Behrens, B.: Superimposed oscillating and non-oscillating ring compression tests for sheet-bulk metal forming technology. In: Advanced Materials Research, 794(2015), Trans Tech Publications, Switzerland, pp. 89-96
2014
- Behrens, B.; Hübner, S.; Bouguecha, A.; Gribic, N; Vucetic, M.: Comparison of determination of biaxial true stress – true strain curves by the use of plane strain compression test and bulge test. In: AIP Publishing, 1567(2014)1, AIP Conference Proceedings , pp. 650-653
2013
- Salfeld, V.; Krimm, R.; Hübner, S.; Vucetic, M.: Sheet-Bulk Metal Forming of Symmetric and Asymmetric Parts. In: Advanced Materials Research, 769(2013), Switzerland: Trans Tech Publication, pp. 229-236
- Behrens, B.; Hübner, S.; Vucetic, M.: Verfahren zur Herstellung eines Bauteils und kombiniertes Umformwerkzeug dafür. In: Patent: WO 2013017659 A1, (2013), published
- Behrens, B.; Hübner, S.; Vucetic, M.: Influence of Superimposing of Oscillation on Sheet-Bulk Metal Forming. In: Key Engineering Materials, 554(2013), Trans Tech Publications, Switzerland, pp. 1484-1489
Presentations
2015
- 26.02.2015: Koch, S.: Prozessauslegung und Untersuchung von geschliffenen und CrAlN / CrAlCN-beschichteten Werkzeugoberflächen mittels schwingungsüberlagertem Ringstauchversuch für die Blechmassivumformung, Dortmund
- 13.04.2015: Koch, S.: Numerical and experimental investigations of a multistage sheet-bulk metal forming process with compound press tools, Graz, Österreich
- 08.09.2015: Koch, S.: Superimposed oscillating and non-oscillating ring compression tests for sheet-bulk metal forming technology, Hamburg
2014
- 09.01.2014: Vucetic, M.: Comparison of determination of biaxial true stress – true strain curves by the use of plane strain compression test and bulge test, Melbourne, Australia
2013
- 23.04.2013: Vucetic, M.: Influence of Superimposing of Oscillation on Sheet-Bulk Metal Forming, Aveiro, Portugal