A5 - Model Adaptive FE-Simulation (funding period 2)
Development of model adaptive simulation techniques for forming processes of complex functional components with complicated design details
Project Status: finished
Last Update: 23.01.2017
Members
Project description
During the first period of this research project, basic techniques to realize model adaptive algorithms in the simulation of forming processes have been developed. Therefore, suitable model hierarchies were defined by using information and results from related subprojects, namely C1 – C4. As a criterion to switch between certain models, goal-oriented a posteriori error estimators for the modeling error based on the “dual-weighted-residual” (DWR) method were derived. Afterwards, these estimators were used in adaptive algorithms to decrease modeling and discretization error in a balanced manner. At last, first investigations concerning dimension adaptivity and transfer of developed tools into commercial finite-element software were carried out.
Visualization of model adaptive simulations. Left hand: Adaptive usage of different material models combined with mesh adaptivity; right hand: corresponding visualization for friction models.
Main goal of the second period is further development and enhancement of the results derived from the first period. This especially contains derivation of a posteriori error estimators for coupled problems based on the DWR method. In this case, the modeling error, which arises from partly or even completely neglecting coupling, should be estimated and finally lead to an adaptive adjustment of coupling with regard to particular requirements. In the end, these techniques should be used in the algorithms for model and mesh adaptivity already developed in the first period.

Preliminary investigation on adaptive discretizations of thermomechanical contact problems.
The second part of this period deals with dimension adaptive algorithms. Therefor, coupling between solid-like-shell- and solid-elements must be realized. However, not only coupling of both element types but also conversion from one type to the other or vice versa must be dealt with. As characteristic for this subproject, the indicator whether to choose one or the other respectively convert from one to the other element formulation is to be set by goal-orientated a posteriori error estimators. The second step then is going to be the development of an algorithm which realizes on one hand the indication of elements and on the other hand the conversion of certain elements. Finally, an application to technological relevant models is preferable.
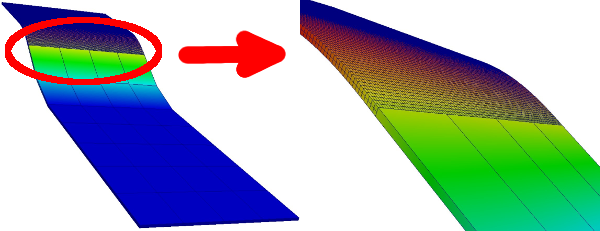
Hybrid mesh containing solid-like-shell and volume elements (left) and a zoom onto the interface of both types of elements (right). Coarse mesh consists of solid-like-shell elements, fine mesh of volume elements.
As an accompanying task during the whole second period, there is the transfer of developed tools to commercial software as well as the assignment to consider modeling approaches from related subprojects C1 – C4.

Model adaptive simulation using Simufact.forming. Left: Friction model distribution within a process of subproject A4. Right: Model error distribution with respect to the differenz between material models provided by Simufact.forming and the developed material model by subproject C3 during a deep-drawing process of subproject A7.
Working Groups
Publications
2016
- Beese, S.; Beyer, F.; Blum, H.; Isik, K.; Kumor, D.; Rademacher, A.; Tekkaya, A.; Willner, K.; Wriggers, P.; Zeller, S.; Löhnert, S.: Simulation of Sheet-Bulk Metal Forming Processes with Simufact.forming using User-Subroutines. In: ESAFORM (Edt.): (2016), Nantes, Frankreich, accepted
- Rademacher, A.: NCP-function based dual weighted residual error estimators for Signorini's problem. In: SIAM Journal on Scientific Computing, 38(2016)3, pp. A1743-1769
- Küstner, C.; Beyer, F.; Kumor, D.; Loderer, A.; Wartzack, S.; Willner, K.; Blum, H.; Rademacher, A.; Hausotte, T.: Simulation-based development of Pareto-optimized tailored blanks for the use within sheet-bulk metal forming. In: Marjanovic, D.; Storga, M.; Pavkovic, N.; Bojcetic, N.; Skec, S. (Edt.): DS 84: Proceedings of the DESIGN 2016 14th International Design Conference, (2016), Design Society, pp. 291-300
2015
- Beyer, F.; Blum, H.; Kumor, D.; Rademacher, A.; Willner, K.; Schneider, T.: Experimental and simulative investigations of tribology in sheet-bulk metal forming. In: Key Engineering Materials, 639(2015), pp. 283-290
- Rademacher, A.: Balancing discretization and numerical error for coupled parabolic hyperbolic problems using the dual weigthed residual method with application to thermoelasticity. In: Ergebnisberichte Angewandte Mathematik (Edt.): Fakultät für Mathematik, TU Dortmund, (2015)516, published
- Rademacher, A.: Mesh and model adaptivity for frictional contact problems. In: Ergebnisberichte Angewandte Mathematik (Edt.): Fakultät für Mathematik, TU Dortmund, (2015)515, published
- Rademacher, A.; Schröder, A.: Dual weighted residual error control for frictional contact problems. In: Computational Methods in Applied Mathematics, 15(2015)3, pp. 391-414
- Rademacher, A.: Adaptive space-time finite element methods for dynamic linear thermoelasticity. In: Proceedings in Applied Mathematics and Mechanics (PAMM) (Edt.): Gesellschaft für Angewandte Mathematik und Mechanik (GAMM), 15(2015), Weinheim: Wiley-VCH Verlag GmbH & Co. KGaA, pp. 681-682
2013
- Schmaltz, S.; Landkammer, P.; Beyer, F.; Kumor, D.; Rademacher, A.; Blum, H.; Steinmann, P.; Willner, K.: Vorstellung eines Simulationsbenchmarks für die Blechmassivumformung. In: Merklein, M.; Behrens, B. A., Tekkaya, A. E. (Edt.): 2. Workshop Blechmassivumformung, (2013), Bamberg: Meisenbach, pp. 53-68
Presentations
2016
- 27.04.2016: Kumor, D.: Simulation of Sheet-Bulk Metal Forming Processes with Simufact.forming using User-Subroutines, 19th ESAFORM Conference, Nantes, Frankreich
- 25.07.2016: Kumor, D.: Dual weighted residual method based error indicators for the local choice of the finite element, WCCM XII & APCOM VI, Seoul, Südkorea
2015
- 26.03.2015: Rademacher, A.: Adaptive space time finite element methods for dynamic nonlinear thermomechanical coupled problems, GAMM
- 29.05.2015: Rademacher, A.: Model adaptivity for frictional contact problems, ICCM, Hannover, Deutschland
- 08.06.2015: Rademacher, A.: Adaptive space time finite element methods for dynamic nonlinear thermomechanical coupled problems, ADMOS, Nante, Frankreich
2014
- 21.07.2014: Rademacher, A.: Model and mesh adaptivityfor frictional contact problems, WCCM 2014, Barcelona, Spanien
2013
- 21.03.2013: Rademacher, A.: Dual weighted residual error control for contact problems based on NCP functions, GAMM, Novi Sad
- 13.05.2013: Rademacher, A.: Dual weighted residual error control for contact problems based on NCP functions, Seminar Numerische Mathematik und Mechanik, Universität zu Köln
- 30.08.2013: Rademacher, A.: Model and mesh adaptivity for frictional contact problems, Enumath, Lausanne